Continuous product management for product and quality planning during the product development process with APQP
APQP (Advanced Product Quality Planning) is part of the American QS9000 standard, and it is an important tool for improving quality management during the product development process nowadays. Failure prevention based on a specific product-related documentation structure, which provides the manufacturer with an overview and with transparency regarding the entire product development process and which is meant to reduce the necessity of later error corrections, is at the very core of APQP.
Process quality and, ultimately, product quality are increased by central planning, management, and monitoring with regard to all project-relevant information. This is aimed at developing and manufacturing the product supposed to be realized in a way that meets customer requirements and expectations as closely as possible and ultimately also at making sure that costs are economical.
Product development phases with APQP
Most product errors occur as early as during the planning and development phases. Therefore, error corrections later on during the sourcing or even more so during the serial production phases are very expensive and require considerable efforts. The automotive and the mechanical engineering industries realized that quite some time ago, and they are trying to counteract costly corrections and adjustments through advanced quality planning. However, many other industries are still having considerable deficits here. As it is generally applicable, APQP is in principle suitable for all sectors and plenty of scopes, though.
APQP is implemented during product development with the aid of proven tools after a thorough analysis. FMEA (Failure Mode and Effects Analysis), QFD (Quality Function Deployment), as well as feasibility and capability assessments are mainly used in practice. Any and all assessments focus on failure prevention. Those efforts will result in fine-grained and detailed QM plans at the group level (assemblies, individual parts, …) as well as at the phase level (prototype, pre-series, series).
Objectives and advantages of APQP
The strict risk assessments and control plans of APQP will help prevent a variety of quality problems before the transition to serial production actually takes place. This won’t merely reduce downstream problems. In addition, it will accelerate the transition to the market launch in general without customer satisfaction being neglected. All the same, improved process control will make it possible to intervene and respond more quickly should any problems arise.
Advantages of APQP
As a structured approach for ensuring product quality during the entire development process, APQP has quite a few advantages to offer:
• Early failure prevention: APQP furthers early identification and correction of potential issues before they turn into big problems, thus reducing the risk of rework and delays. Since risks can be identified and assessed in advance, the respective measures can be taken in order to minimize those risks.
• Fulfillment of customer requirements: Systematic planning and assessments ensure that any and all customer requirements and specifications are met, increasing customer satisfaction.
• Improved communication: The structured approach promotes better communication and cooperation between and among different departments and suppliers, leading to a smoother development process.
• Cost efficiency: Costs can be lowered due to prevention of failures and delays, as there will be less rework and fewer quality problems.
• Documentation and traceability: APQP provides for clear documentation of any and all steps and decisions during the development process, facilitating traceability and evaluation.
• Improved product quality: The structured process ensures that products meet the established quality standards, enhancing overall efficiency and overall quality.
• Continuous improvement: APQP furthers a culture of continuous improvement, as the process involves assessments and adjustments on a regular basis.
Disadvantages of APQP
Despite those many advantages, APQP also needs to overcome some challenges during its practical application, of course:
• High effort and complexity: Implementing APQP may be time-consuming and complex, especially when it comes to companies that have no established processes in place yet. The necessity of creating detailed documentation and engaging in comprehensive planning may require additional resources. Monitoring and documenting the different phases on a continual basis may increase administrative effort and entail additional administrative tasks.
• Costs: Introducing and maintaining an APQP system may go together with additional costs, especially for training, tools, and additional working hours. Coworkers need to be trained in order for APQP to be used effectively. This may take up additional time and resources. A lack of well-qualified professionals may negatively affect quality and efficiency.
• Resistance to change: Coworkers or departments might resist, especially if they cling to existing processes or don’t understand the necessity of performing APQP. This can make it more difficult to implement APQP successfully.
• Dependency on correct implementation: The success of APQP heavily depends on its proper implementation and consequent application. A lack of discipline or incomplete performance may affect effectiveness adversely. The structured nature of APQP might, in certain cases, limit flexibility, though, especially when it comes to quickly changing requirements or innovative projects that require rapid adjustments.
APQP 3rd Edition: What does the newest version of APQP offer?
Revising the APQP, which is now available in its 3rd edition, was necessary for meeting changing industry requirements and for improving quality assurance in increasingly more complex and globalized surroundings. The most remarkable change in the 3rd edition of the APQP manual highlights the robustness of management activities.
Sourcing risk analyses, change management, APQP program metrics, risk assessments, and gated management play central roles there now.
However, the issue of control plans was removed, and it is now available as a standalone manual, also in a revised edition.
Consulting on APQP
PeRoBa GmbH München is offering comprehensive consulting services on the issue of APQP for small and medium-sized enterprises. We are mainly focusing on the automotive industry, but we are also working across sectors. Depending on your requirement profile, we can offer you the following partial services from a single source:
- Analyses of your present process quality and your need for APQP
- Consulting on APQP introduction strategies for your planning and manufacturing processes
- Training and workshops on APQP
- Project and product reviews
- Creation of manuals and QM plans
With APQP Consulting by PeRoBa GmbH München, you are laying an important foundation for long-term customer satisfaction. Quality products and moderate cost levels are not mutually exclusive – they are the results of proactive planning as well as of consistent and systematic quality management over the entire product cycle.
Frequently asked questions on the issue of APQP
What is APQP?
What is the purpose of APQP?
What are the Core Tools?
What phases does APQP provide for?
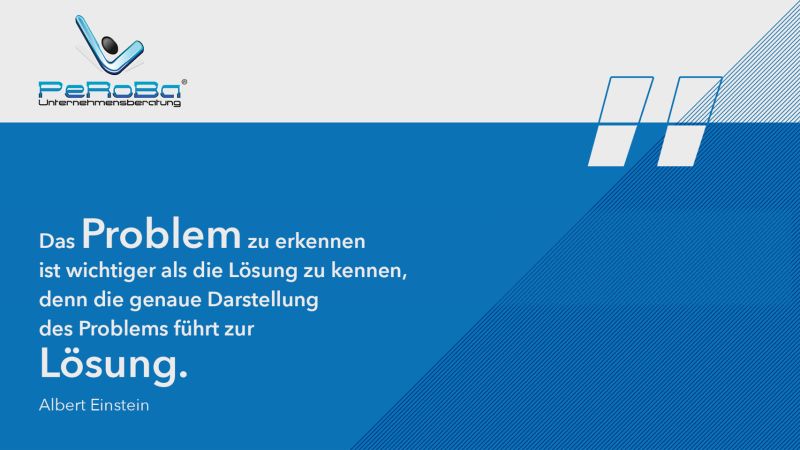

Looking for consulting on APQP? We can help you.
Arrange a non-binding initial consultation via online appointment, or send us a message using the contact form. You are also welcome to contact us by telephone.